Milling Bur
- Full Spectrum
- All your CAD/CAM milling bur needs covering
- Customization services are offered upon request.
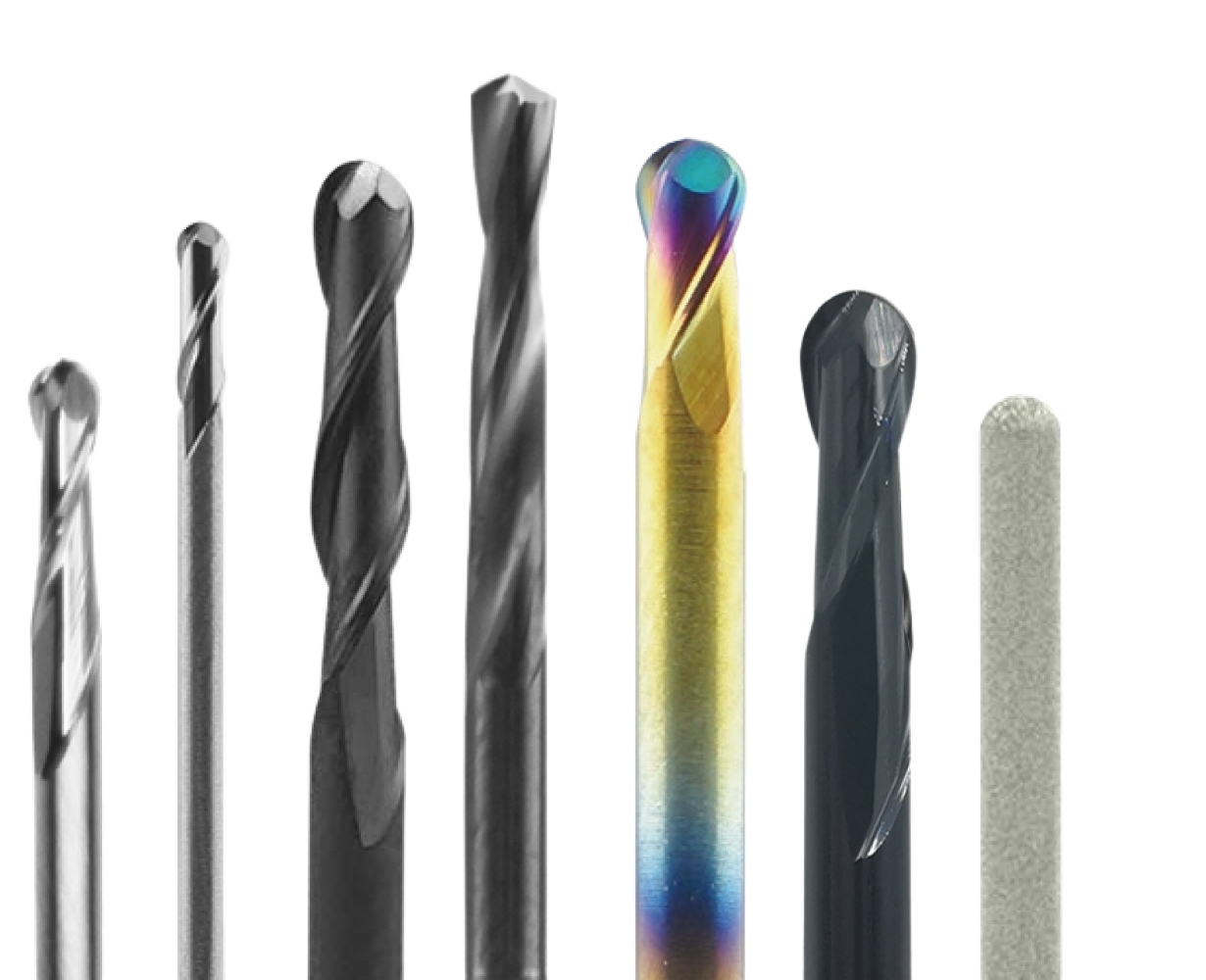
Indication
Specialized dental milling burs feature a semi-circular adhesive. The milling range spans from 0.3mm to 2mm, suitable for preliminary and efficient manufacturing. The 0.6mm milling bur is primarily used for sculpting grooves, enhancing craftsmanship precision. Due to the milling bur’s unique length and flexible milling capabilities, occlusal issues can be easily addressed.
Our tungsten carbide milling burs, compatible with mainstream CAD/CAM machines or systems, are good choices for trimming zirconia, porcelain, PMMA,Wax, Peek, titanium, cobait-chromium alloy, titanium alloy, glassceramic and ect. Customization services are offered upon request.
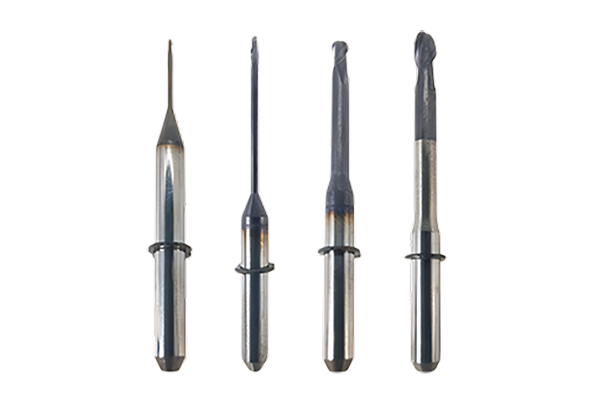
Advantage
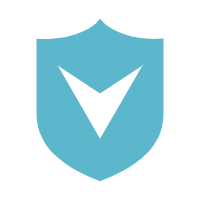
Stable quality
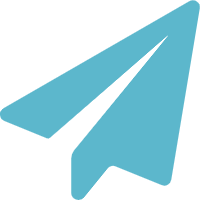
High efficiency
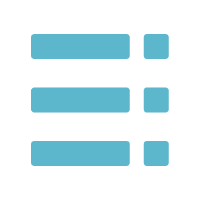
Full spectrum
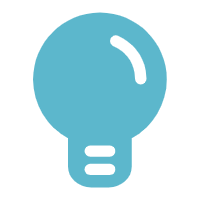
Long service life
CAD/CAM size & coating of milling burs
Our tungsten carbide milling burs, compatible with mainstream CAD/CAM machines or systems, are good choices for trimming zirconia, porcelain, PMMA, Wax, Peek, titanium, cobalt-chromium alloy, titanium alloy, glass-ceramic and etc. Customization services are offered upon request.
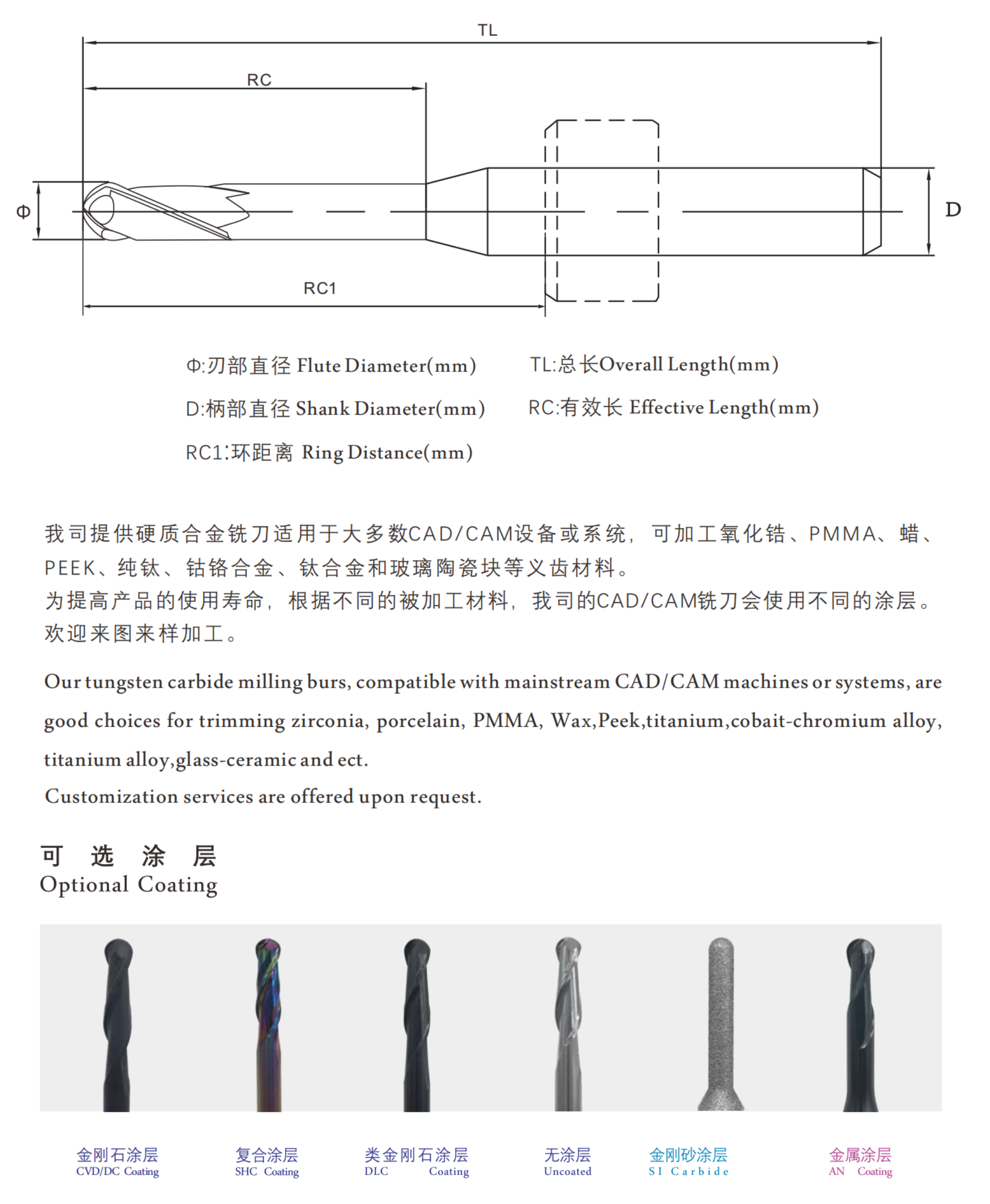
Optional Coating
- CVD/DC Coating
- SHC Coating
- DLC Coating
- Uncoated
- SI Carbide
- AN Coating
Product list
CAD/CAM Cutting Burs
- XTCERA
- IMES-ICORE
- ARUM
- IDEAL
- ZOTION
- BSM
- UP3D
- JINY
- CRADLE
- RK
- DEMETDENT
- LNY
- KAVO
- SIRONA
- UPCERA
- DENTIUM
- ROLAND
- AMANN
- ZIRKONZAHN
- CERCON
- WIELAND
- VHF
- AIM
- CAMEO
- LAVA
- YENADENT
- AIDITE
- ELOSDENT
- IVOCLAR
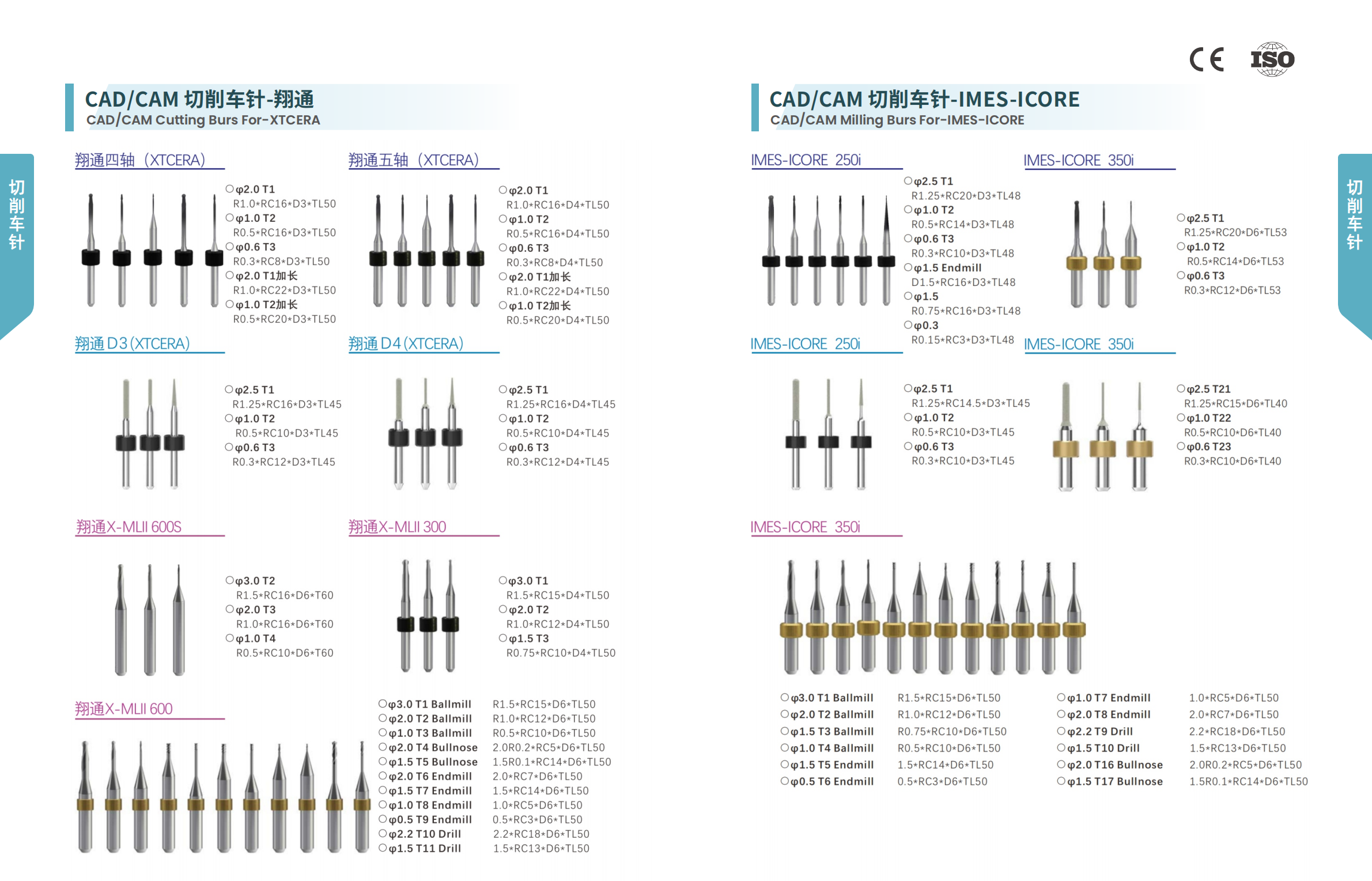
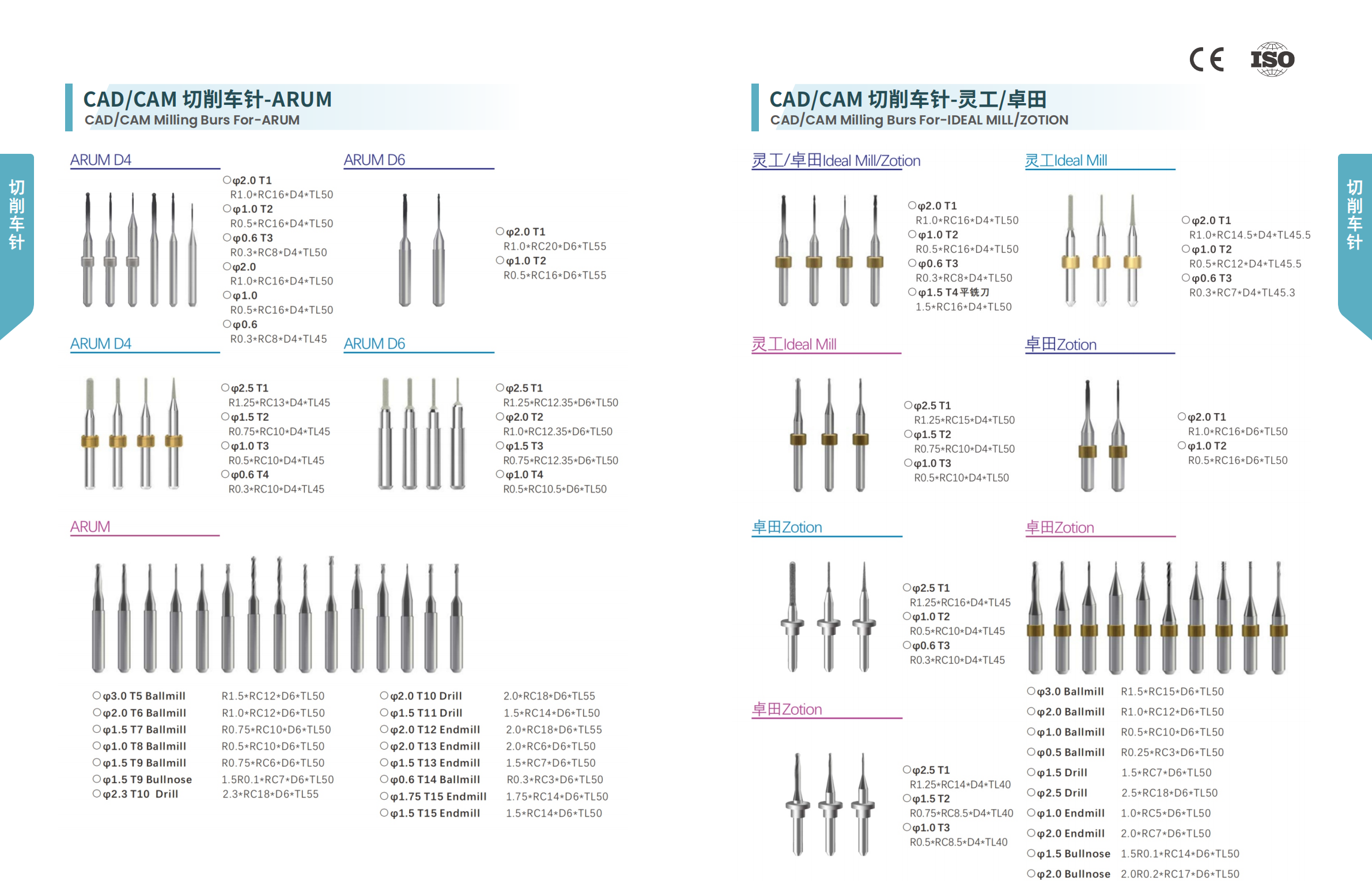
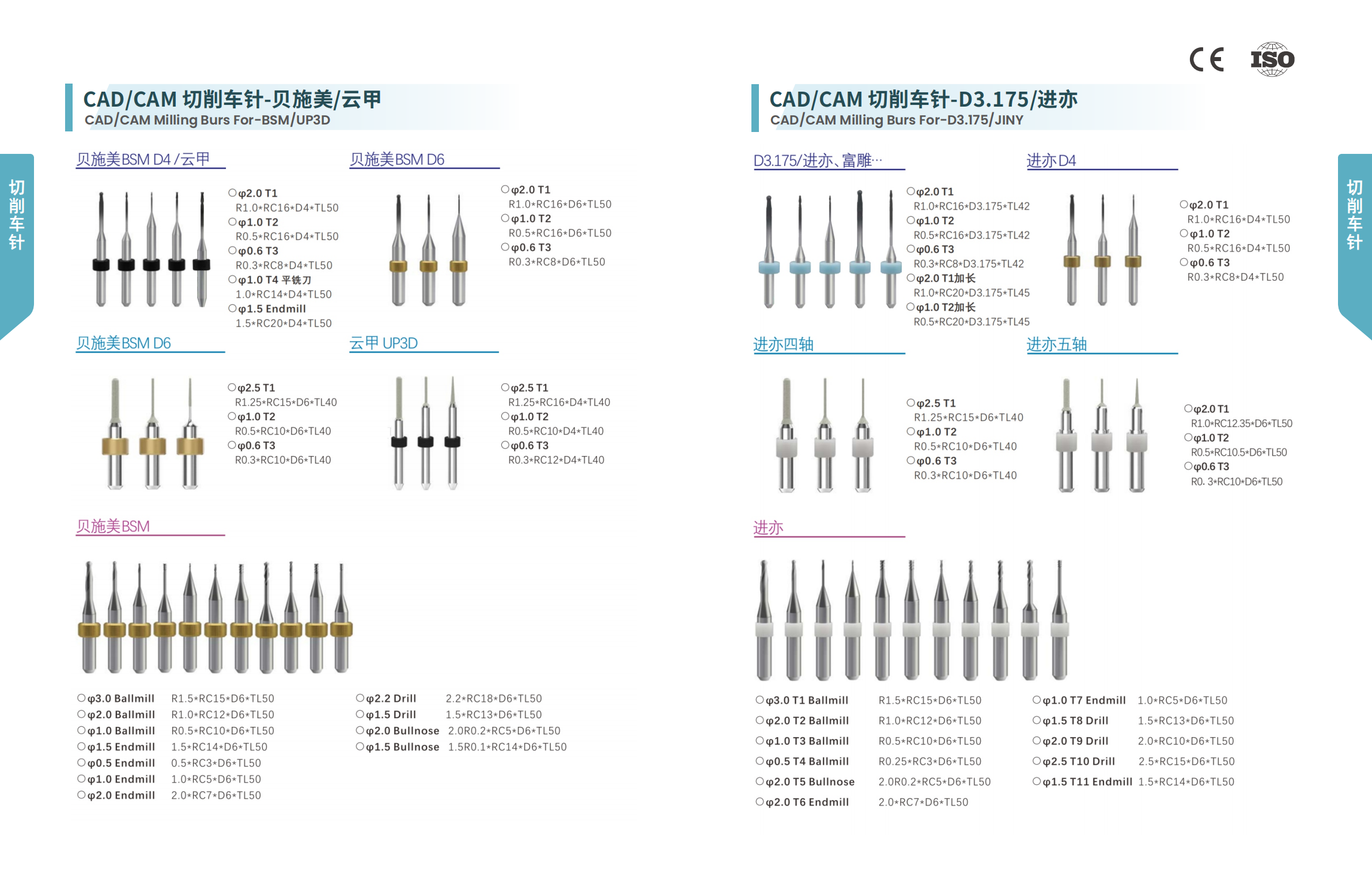
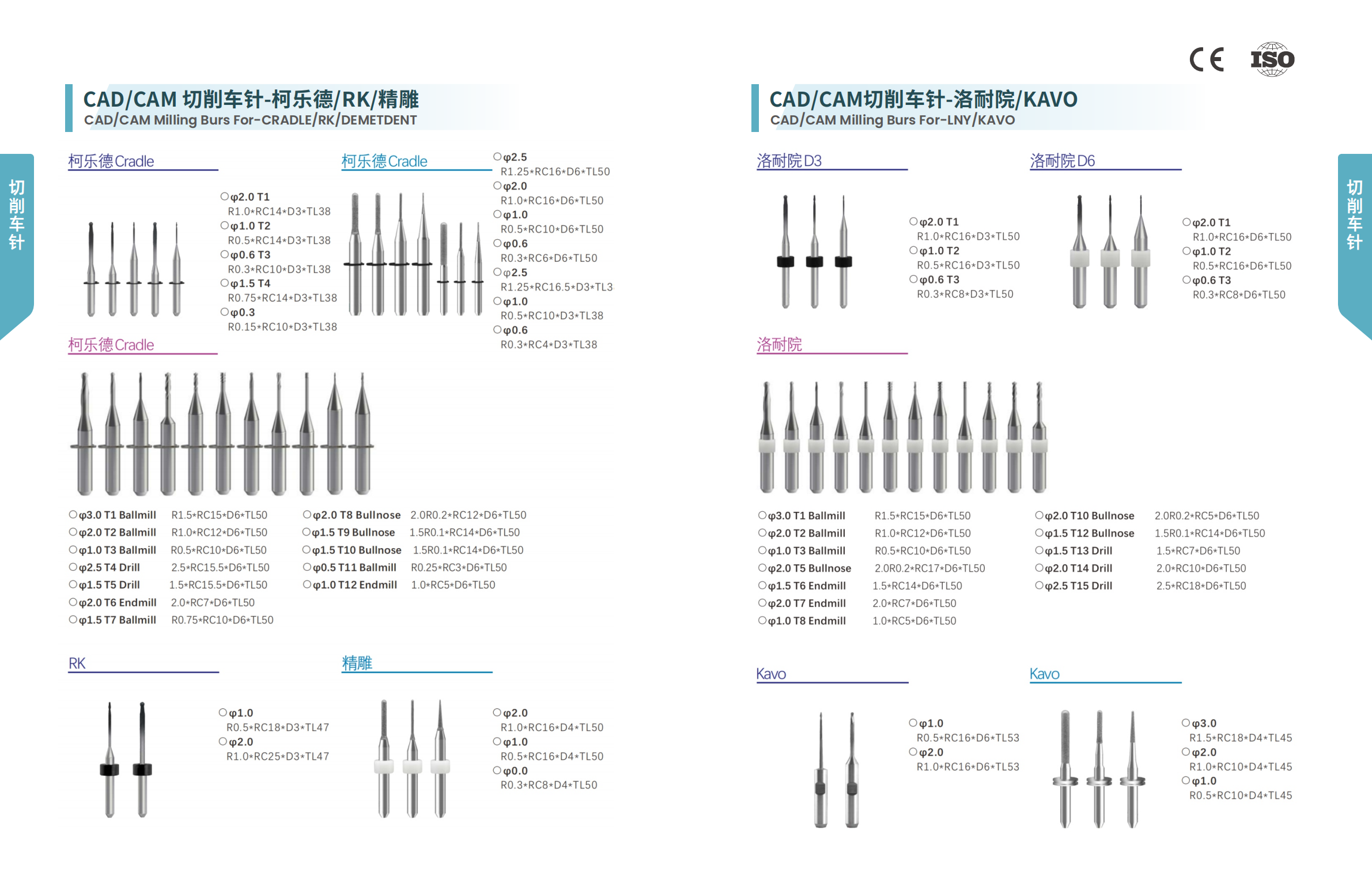
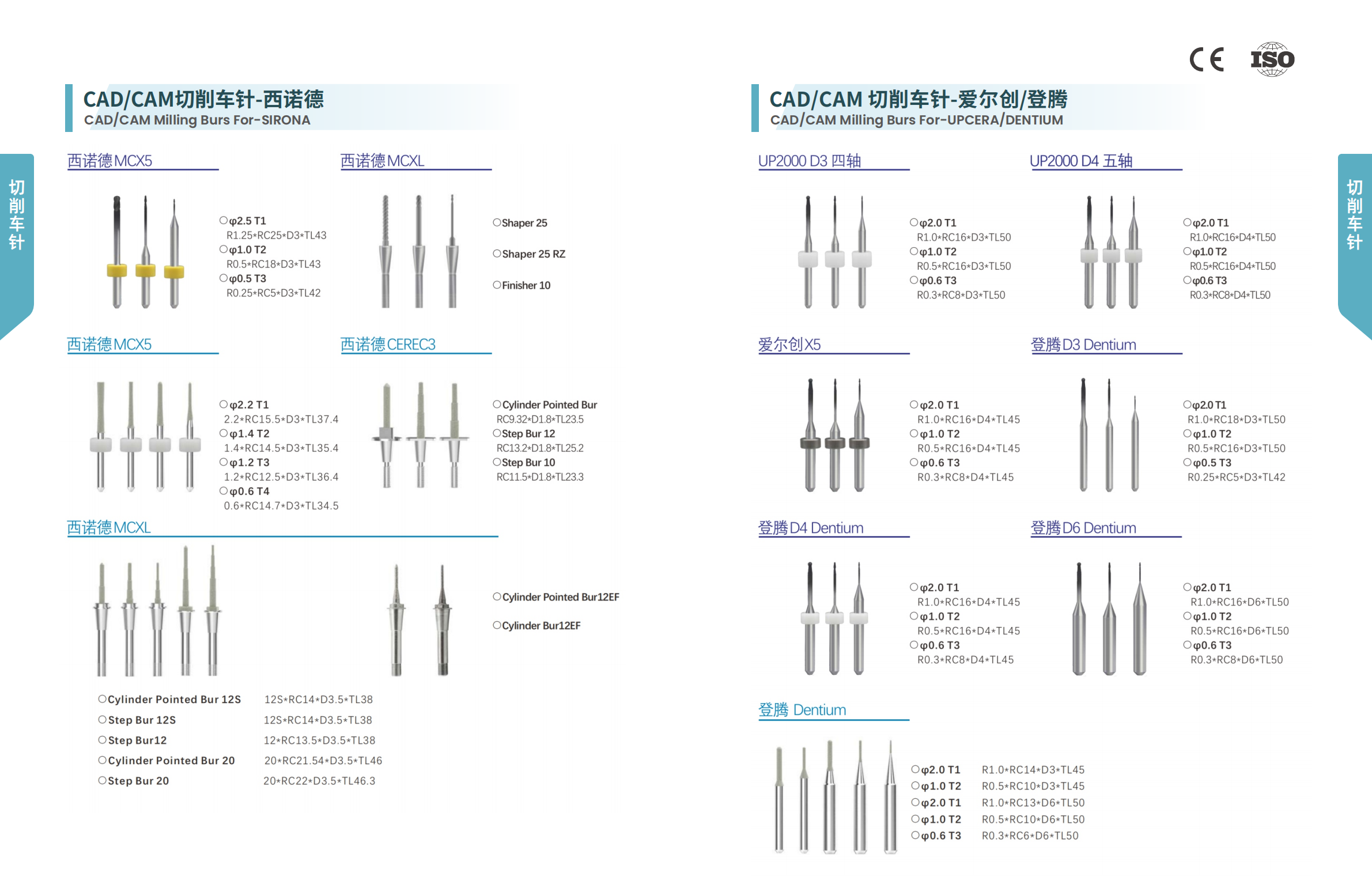
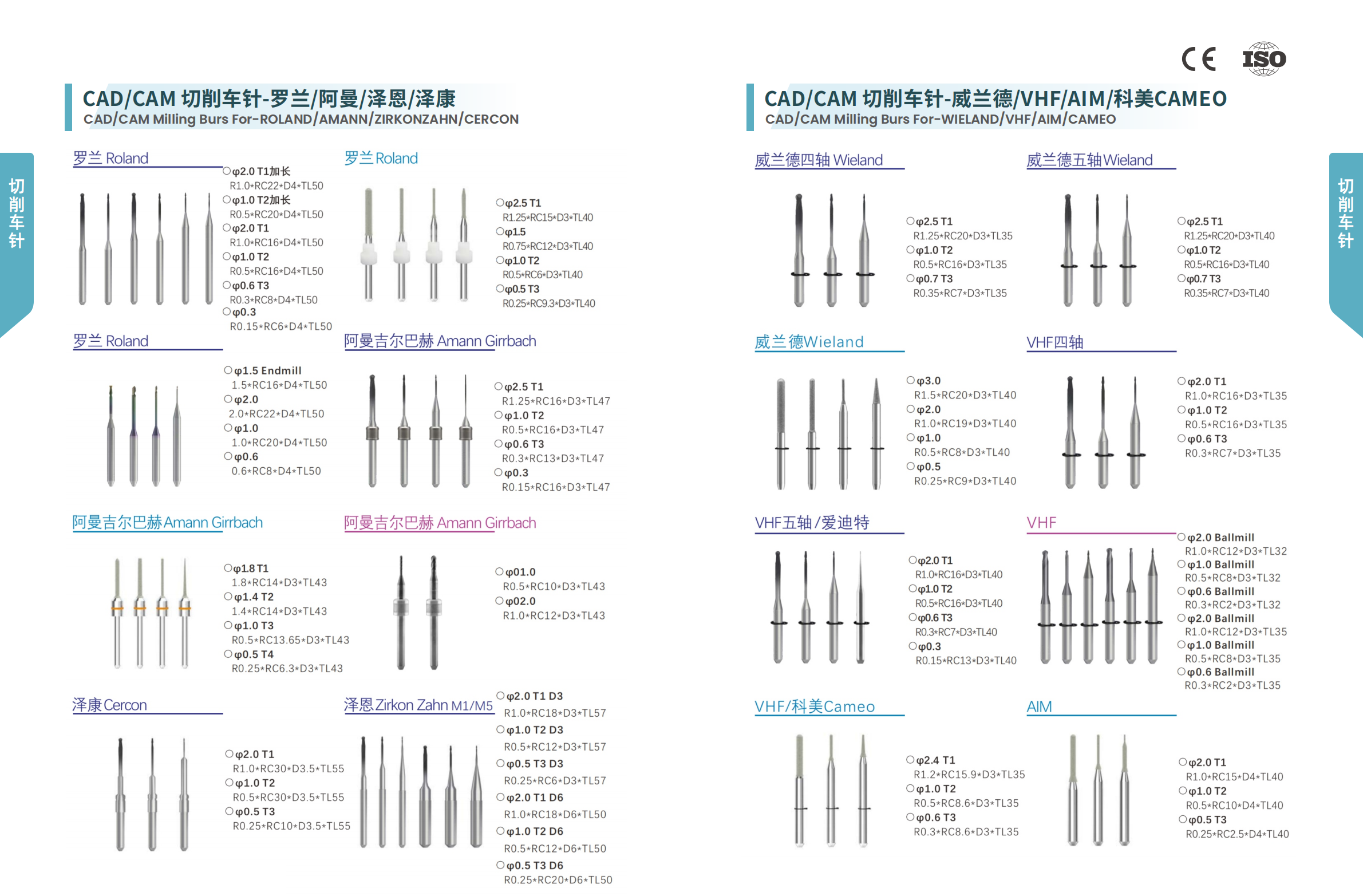
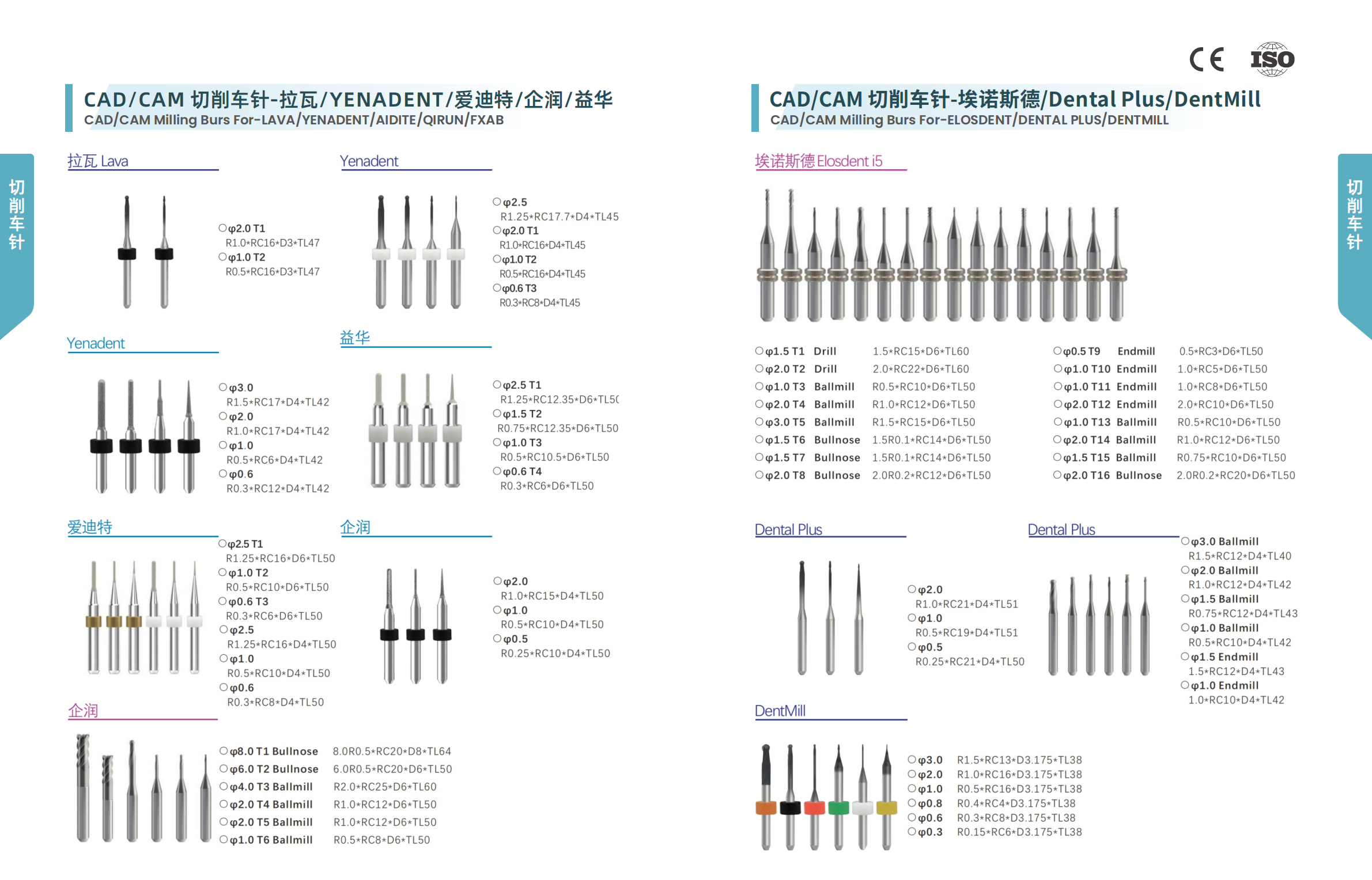
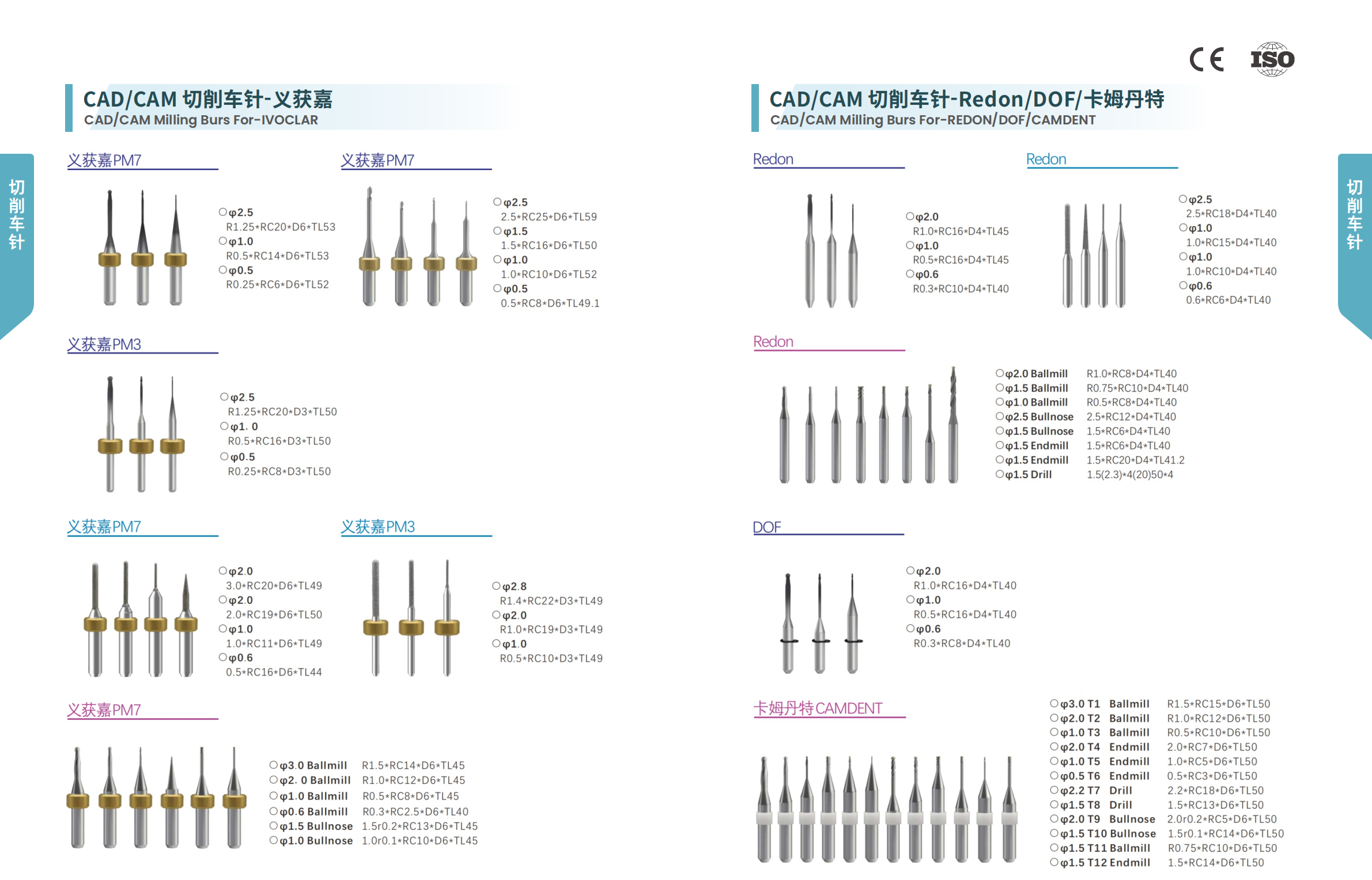
Tungsten Carbide Milling Instument
Tungsten Carbide Dental Lab Rotary Burs-Cross Cut
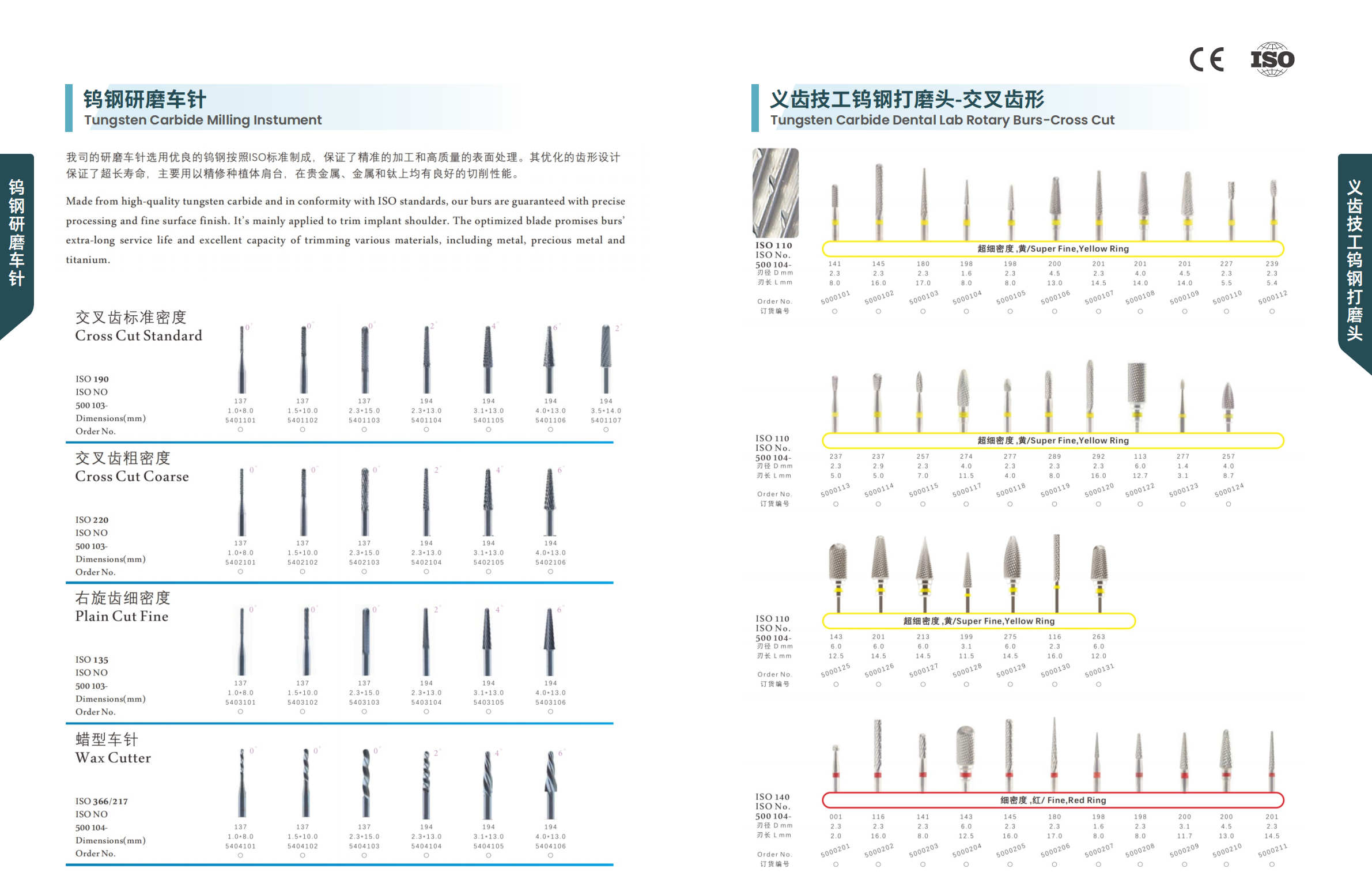
Tungsten Carbide Dental Lab Rotary Burs-Cross Cut
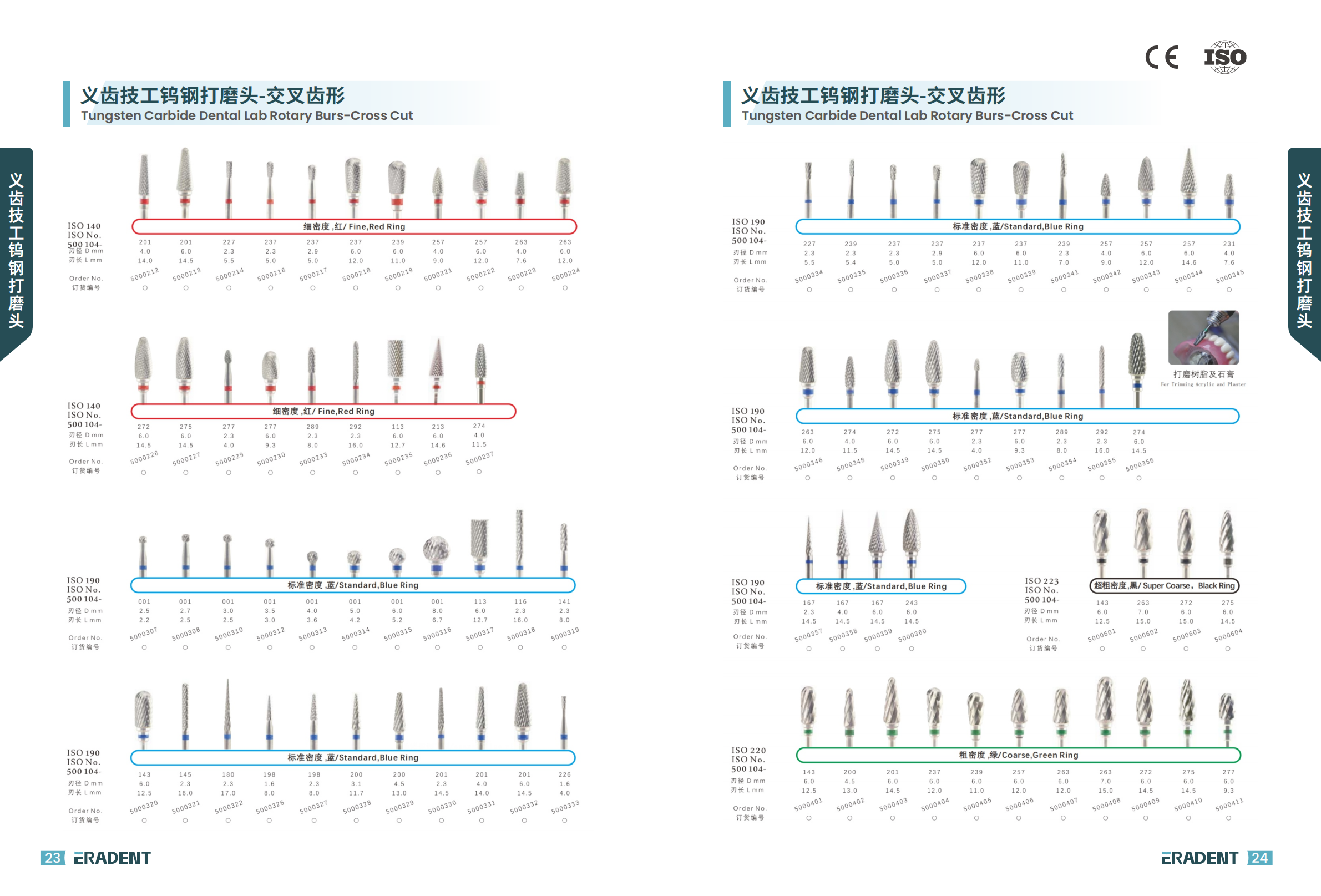
Tungsten Carbide Dental Lab Rotary Burs-Plain Cut
Tungsten Carbide Dental Lab Rotary Burs-Spiral Cut
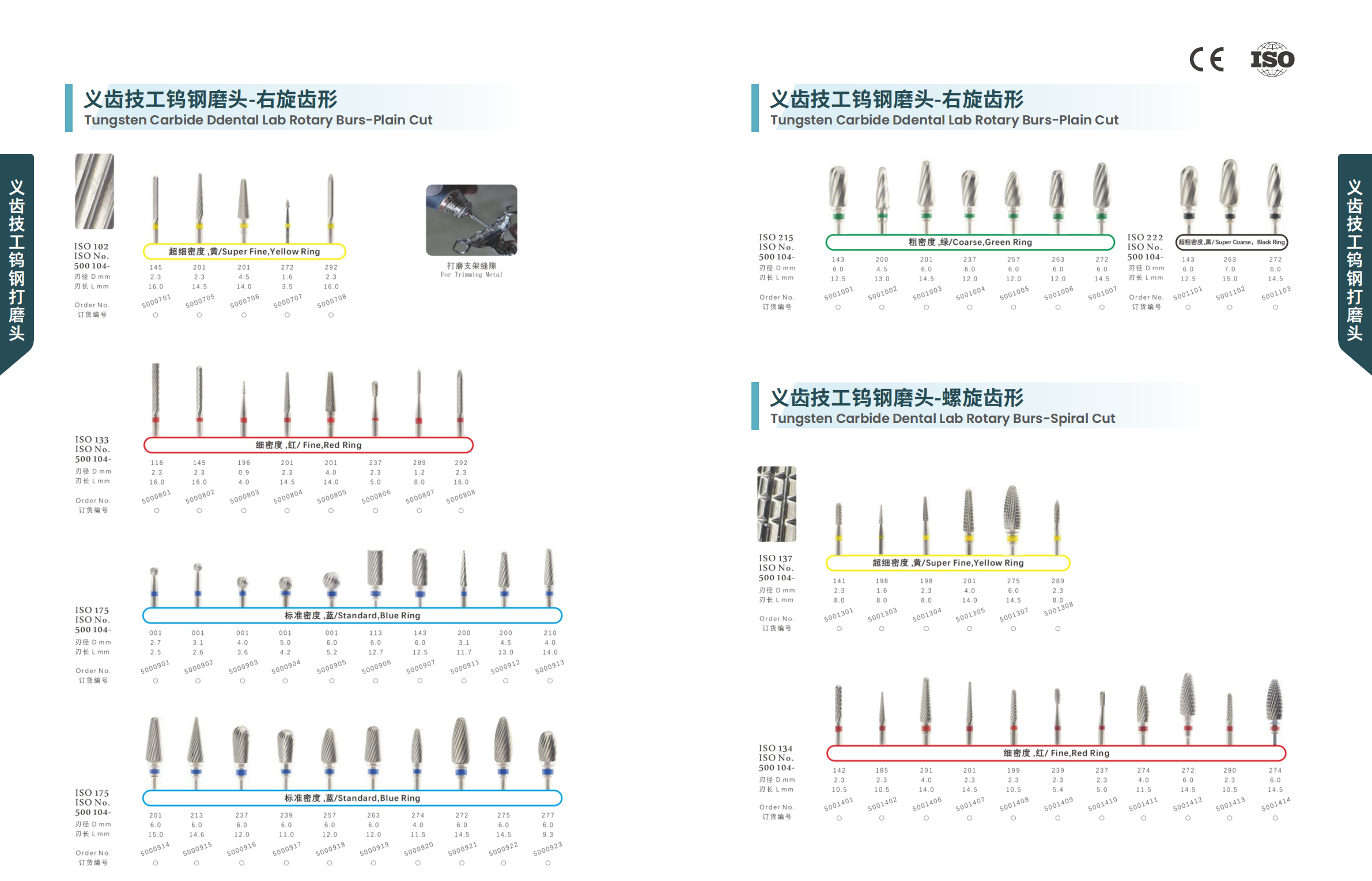
Tungsten Carbide Dental Lab Rotary Burs-Straight Edge With Spiral Cut
Tungsten Carbide Dental Lab Rotary Burs-Diamond Cut
HP-Diamond Bits With Cooling-Groove
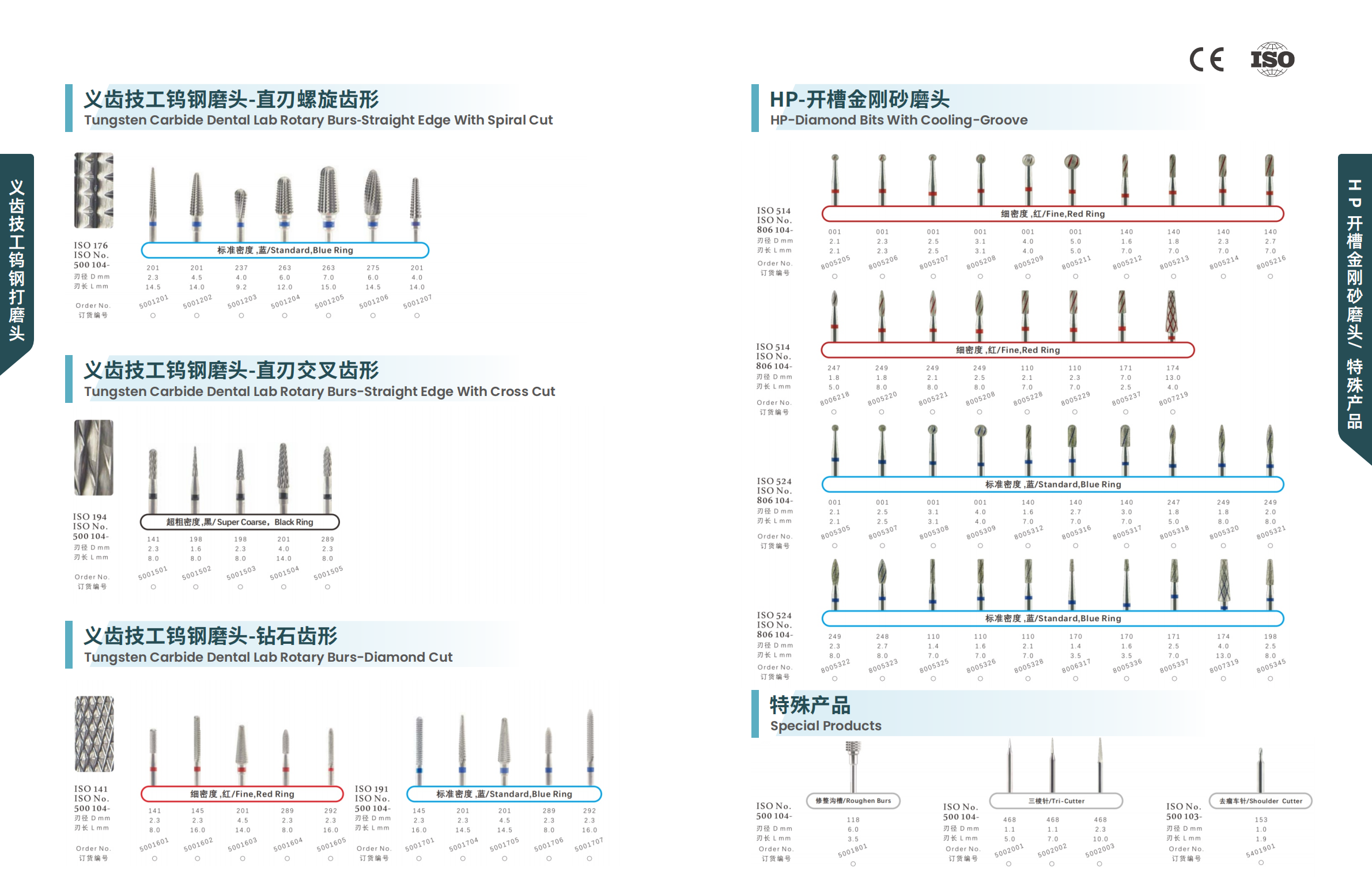
1. The three-petal spring chuck has been used for a long time, and the inner wall is worn, causing the spindle chuck to loosen;
2. When changing the tool or in the process of operation, the air pressure is unstable or insufficient for a moment, resulting in insufficient chuck pressure; check the air pressure displayed on the cylinder pressure gauge, the air pressure should be at least 6.5;
3. The position of the needle limit ring is offset
Solution:
1. Please use professional tools to remove the chuck, clean it, oil it and tighten it again. If the inner wall is severely worn, the chuck should be replaced;
2. If the limit ring is displaced, use a caliper to measure the height of the limit ring. It can be used only after confirmation. If the limit ring is damaged, replace the needle with a new one.
3. Check that everything is correct and recalibrate the lathe before you can start working.
1. Check whether the needle is worn and whether the edge of the tooth design data is too thin.
(1) The needle blade may break due to collision or poor storage. The broken blade is very small and cannot be seen from the outside.
(2) The processing volume and working time of the same batch of needles have reached the end of the needle life, and the needles need to be replaced
2. If the edge is still broken after replacing the new tool, you need to calibrate the equipment again (with a new needle) and check the data
3. If the equipment continues to collapse after calibration, the processing strategy and processing materials need to be confirmed again.
4. If the processing strategy is correct, but edge collapse still occurs after replacing the new material, the old material can be used for testing and the corresponding problem can be eliminated.
5. A single undercut is too large and exceeds the cutting capacity
(1) Machine tool work authority value
(2) Maximum working limit of the tool
6. Device software error
Solution:
Start with the size and amount of chipping. Generally, factories will not change materials casually, so start with tool inspection, then do the corresponding daily maintenance of the equipment and calibrate the equipment regularly. Simple equipment problems are also within the scope of daily supervision and maintenance. Be patient and careful to avoid blind operation that may cause damage to the equipment. (Remember: professional equipment needs to be maintained and used by professionals)
1. The needle material is not tough enough
2. The air pressure is unstable or insufficient at the moment, resulting in insufficient chuck pressure; check the air pressure displayed on the cylinder pressure gauge, the air pressure should be at least 6.5
3. Exceeding the processing limit (undercut is too large)
4. For equipment with adjustable processing templates, the cutting depth is too large
5. Incorrect or unstable typesetting and corresponding processing strategies
6. The developmental groove is designed too deep, exceeding the working limit of the needle (this is easy to happen for the smallest fine needle of R0.3)
Solution:
The needle will not break if it is not subjected to excessive external force. When using the equipment, you must be familiar with the working capacity of the equipment and operate it correctly. If large-scale needle breakage occurs due to changing the needle manufacturer, you should first determine the problem of needle quality.
1. Design parameters are too large
2. Hardware problems such as equipment axial/screw
3. When the equipment software does not have tool wear compensation, it will appear when using a new needle
4. Zirconia material shrinkage ratio
Solution:
The internal crown void is usually caused by high bite, so different parameters can be set by the same restoration to select the appropriate
If the result is too different from the model (excluding the “3D” printed model), the jaw design parameters are too different from the model.
After the accuracy is determined, the crown can be cut in the buccal-lingual or mesio-distal direction. Measure the thickness of the same position point by point and compare it with the designed main component value. If the lathe still cannot meet the standard after recalibration, please contact the equipment manufacturer for repair.
1. Design data/bonding parameters
2. Scanning error
3. Tool damage
4. Zirconia material shrinkage ratio
5. Equipment spindle/screw problem
6. Crystallization temperature is too high
Solution:
When a crown is too tight, the first thing that comes to mind is the problem of the turning needle. The design should be put first during the analysis. The main reason is that regardless of whether it is an inner or outer single, the tooth length and degree of polymerization are not the same, and the number of abutment teeth is more or less. Under the premise of assuming that they are unchanged, using the same parameters, some crowns are tight while others will definitely not be able to fit in place directly; shallow crowns have a large degree of polymerization, so the parameters are small; long crowns have a small degree of polymerization, so the parameters are large; the more teeth there are, the larger the parameters should be under the above premise; the crystallization temperature is too high, you can consult the corresponding material supplier.
1. The step distance of the lathe does not match
2. The tool is damaged
3. The typesetting calculation is incomplete
4. Equipment failure
Solution:
It is recommended to choose a processing equipment brand with good stability and performance, and it should be avoided if it is used correctly and reasonably.
1. Decreased equipment stability
2. Needle damage
3. Hidden cracks caused by separation of restorations
4. Hidden cracks caused by external forces
5. Hidden cracks caused by improper baking
6. Hidden cracks caused by too fast heating rate during sintering
Solution:
Replace the new needle and calibrate the equipment in time, and perform regular maintenance and upkeep of the equipment; handle the restoration with care during operation, lower the speed and reduce the pressure when separating the restoration; sinter strictly according to the sintering curve of each porcelain block manufacturer during sintering; the furnace temperature is -1530℃. If the temperature is not reached or the temperature is too high and the tooth is taken out of the furnace without cooling, the sintered tooth will have hidden cracks.